Hydrogen as an energy source
Hydrogen as a future energy source
Hydrogen is one of the great beacons of hope for a climate-neutral energy transition. It is light, can theoretically be transported and stored in the existing gas infrastructure, can be used as an intermediary for energy conversion as well as an end product and releases few to no emissions depending on the type. For example, in nature it is present bound with oxygen (O2) to form water (H2O) or also in the form of hydrocarbons in methane (CH4) or oil.
The colours of hydrogen
Although colourless at first glance, hydrogen is in fact a colourful element whose ‘colour’ is determined by the energy sources used during production. The following provides a brief summary of useful information about the different colours of hydrogen and their association with specific production methods.
Electrolysis – how water and electricity is used to produce green hydrogen
In nature, hydrogen is only present as a bonded carrier. As a result, it needs to be split using primary energy. At the moment, over 90% of hydrogen is produced through steam reforming, i.e. using natural gas. Besides this, initial methods for producing hydrogen from biomass using (hydrothermal) gasification already exist. In view of the increasing, politically supported production of renewable electricity, e.g. using wind power, many consider (water) electrolysis to be an attractive option for producing hydrogen.
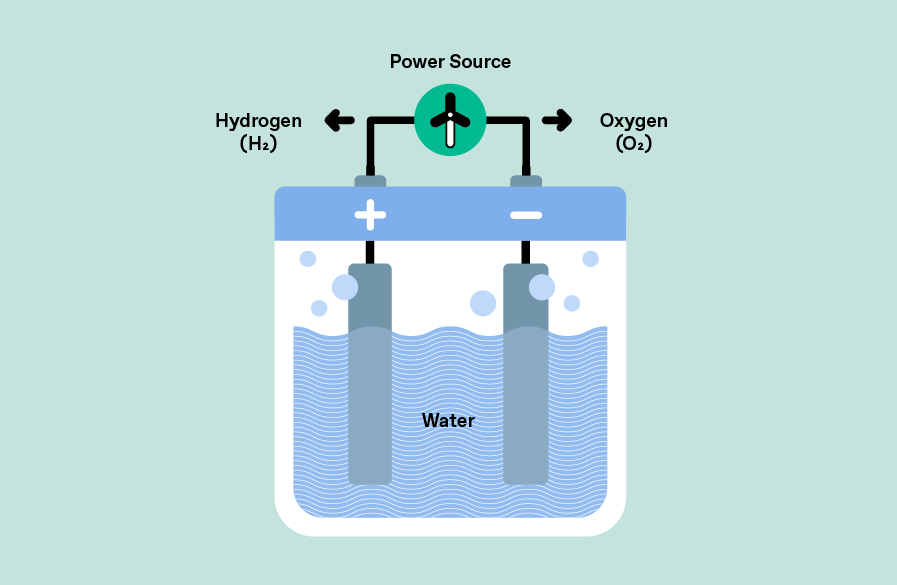
In electrolysis, an electrolytic cell is used to split water (H2O) into its constituents hydrogen (H2) and oxygen (O2) using an electrical current source. Current is applied to two electrodes: oxidation takes place at the anode to produce oxygen, while reduction takes place at the cathode to produce hydrogen. The oxygen produced is allowed to dissipate, while the hydrogen is collected for further use. The use of renewable energies (solar or wind) makes the entire process sustainable and leads to the production of green hydrogen.
Types of electrolysis
Different methods may be used to electrolyse water to produce hydrogen:
Alkaline electrolysis (AEL)
AEL is the oldest electrolysis technology. Two, usually nickel-based electrodes, are separated from each other by a porous diaphragm. When voltage is applied, water (H2O) gains an electrode to form hydroxide ions (OH-) and hydrogen (H2) at the cathode. Due to their negative charge, the hydroxide ions move through the membrane towards the anode where they lose an electron and react to form oxygen (O2) and hydrogen (H2). At the same time, the membrane is impermeable to gas and so prevents oxygen from mixing with the hydrogen.
The primary benefit of AEL is the low investment costs thanks to the technical maturity of the method. In addition, this type of electrolysis ensures the long-term stability of the cell and uses few to no critical resources. However, particular disadvantages are the high technical requirements associated with the method and the long cold start-up time, meaning that fluctuating electricity sources, such as wind energy, are problematic.
Polymer electrolyte membrane electrolysis (PEM)
In this case, as the name suggests, a polymer electrolyte membrane (PEM) is used in the electrolytic cell. This enables the charged protons on the anode side to be transported to the cathode side where they diffuse, and simultaneously prevents the penetration of gases. Green hydrogen is currently predominantly produced using PEM electrolysis.
The benefits of PEM electrolysis are its efficiency, high power density, precise control and speed of reaction. Conversely, PEM electrolysis can react sensitively to impurities and certain environmental conditions, which can lead to performance losses. In addition, the use of platinum or iridium catalysts in particular is associated with high costs. As a result, activities are currently focussed on developing alternative catalysts.
Anion exchange membrane electrolysis (AEM)
AEM electrolysis is based on the AEL principle, but uses an anion exchange membrane as an electrolyte instead of an alkaline solution. The membrane is permeable for the negatively charged hydroxide ions and also blocks the passage for the positively charged hydrogen ions so that they can be separated.
This method has the benefits of lower operating costs due to the absence of expensive precious-metal catalysts and the option of using non-alkaline electrolytes. However, this technology is still under development and there are challenges with regard to the long-term stability of the membranes and the reaction efficiency.
High-temperature (solid oxide) electrolysis/solid oxide electrolysis cell (SOEC)
High-temperature electrolysis makes use of a ceramic solid state electrolyte, typically yttria-stabilized zirconia. An anion exchange membrane separates the cathode and anode from each other. The cathode consists of porous materials, such as nickel and a metal-ceramic bond, while the anode consists of a perovskite crystal. A gas diffusion layer prevents unwanted reactions between the materials. HT electrolysis typically takes place at 800°C to 1200°C. It is particularly suitable for industrial sites with existing high-temperature waste heat.
The great benefit of HT electrolysis is its low energy consumption and the higher efficiency at higher temperatures. The minimum voltage required to split water into oxygen and hydrogen is lower at higher temperatures, resulting in more efficient operation. However, HT electrolysis is still in the pilot phase and has not been implemented on a major industrial scale to date.
Storing hydrogen
The future is clear: a climate-neutral and secure energy supply. This makes storage facilities absolutely critical. For instance, in Germany, large amounts of renewable energy can be produced during the windy and sunny months but the greatest overall consumption occurs in the other months, when it gets dark early and it’s cold outside. Gas storage facilities have the greatest potential in this area, as only they allow large amounts of energy to be stored over extended periods. This enables different levels of utilisation, whether over the course of the day or depending on the season, to be controlled.
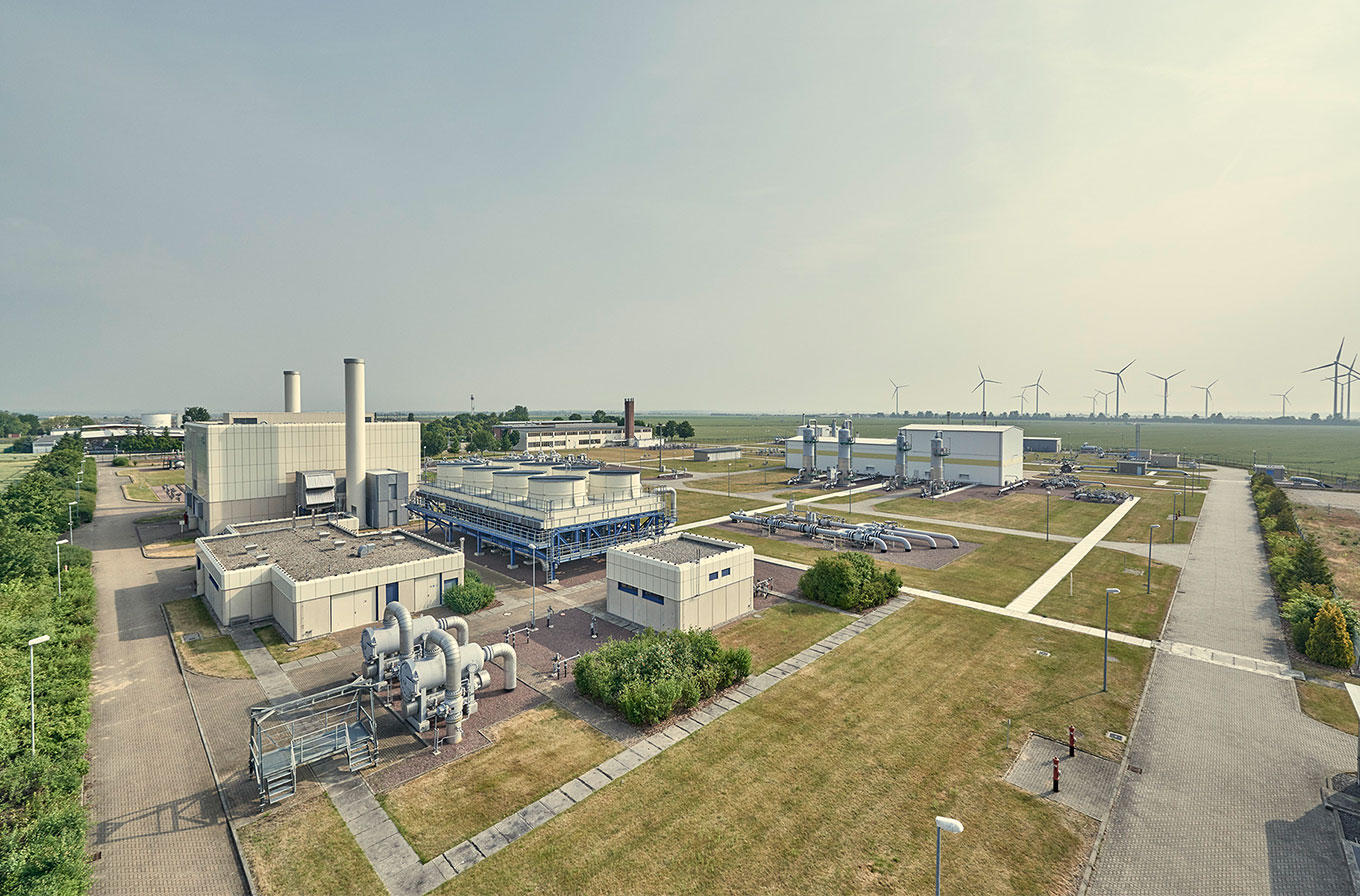
In particular, regions that largely use concentrated, energy-intensive production that is difficult or impossible to electrify (such as the steel or chemical industry) require a hydrogen storage solution in the near future. This will allow weather-dependent fluctuations in wind and solar electricity generation to be countered while also guaranteeing the consistent and reliable availability of hydrogen for industrial consumers. Small above-ground gas storage facilities exist for small-scale local compensation processes. But a long-term energy supply independent of location requires underground storage in the form of salt cavern or porous storage facilities.
Eastern Germany has 5 potential areas with salt caverns that are available for potential use. The geological features and large storage capacity make them ideal for hydrogen storage. Two hydrogen cavern storage facilities are currently under construction in Rüdersdorf near Berlin (EWE) in Brandenburg as well as in Bad Lauchstädt (VGS) in Saxony-Anhalt. The latter has a working gas volume of 50 MCM, roughly 5,000 tonnes of hydrogen. For Germany as a whole, the Gas Infrastructure Europe (GIE) association puts the storage potential in caverns at 40 TWh of hydrogen. This also makes it possible to temporarily store any hydrogen imports.
Types of storage
Gas can be stored in natural or artificial cavities underground: in cavity storage facilities (caverns) or porous reservoirs.
Salt cavern storage
Salt caverns are large, artificial, cylindrical cavities created by the targeted leaching (brining) of salt domes using water. They can have a diameter of up to 100 metres, be between 50 and 500 metres high and have a volume of up to 800,000 cubic metres. The petrochemical properties of salt eliminate the need for any additional sealing of the caverns. At depths of 800 to 1,500 metres, maximum pressures of around 200 bar can be achieved. These properties enable the storage of large volumes of gas as well as rapid addition to/removal from storage. This makes these storage facilities particularly suitable for managing short-term, high demand fluctuations. As hydrogen does not react with the salt rock, salt caverns are ideal hydrogen storage solutions. These types of storage facilities predominantly exist in Northwest Germany and Central Germany.
According to current calculations, the costs for converting a cavern storage facility to hydrogen storage amount to just 30 percent of the costs needed to build a new cavern storage facility and require a lead time until use of five rather than ten years. Extrapolated to include all existing cavern storage facilities in Germany, a conversion to hydrogen storage would require an investment of around 6.5 billion euros by 2030 and 30 billion euros by 2050. By comparison: storing the same amount of energy in the form of a battery storage facility would cost 100 times more.
Porous reservoirs
Porous reservoirs are natural sandstone formations with cap formations impermeable to gas, which have the capacity to store large volumes of gas. Besides aquiferous rock formations, exhausted oil and natural gas storage reservoirs are also used. However, the solubility of hydrogen and gas mixtures in water and the geochemical interactions with the rock currently make such reservoirs unsuitable for storing hydrogen. This type of storage facility is predominantly present in Southern Germany.